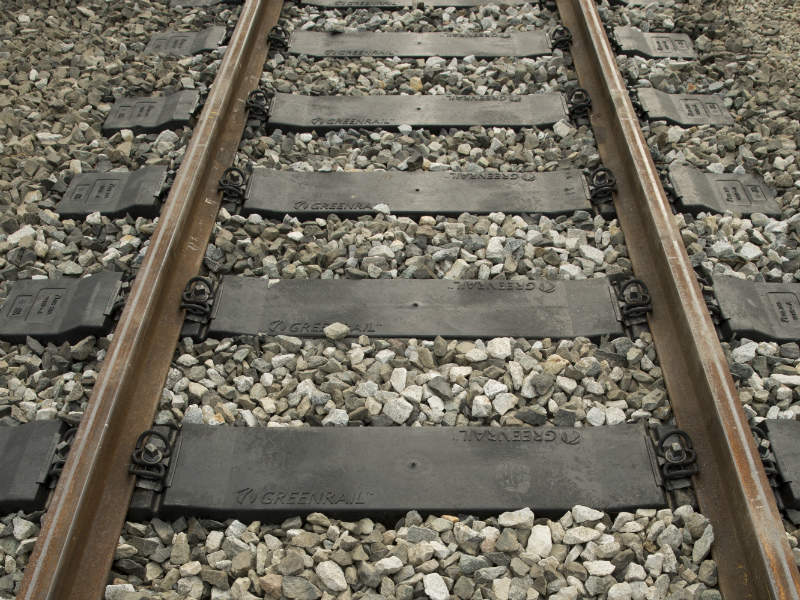
An Italian startup backed by EU funding hopes to revolutionise the railway industry by turning its tracks into clean energy powerhouses.
Railway sleepers usually consist of energy-intensive concrete but Greenrail’s version has an inner concrete core and an outer shell made from a combination of recycled plastic and rubber, collected from end-of-life tyres (ELT). This means that for every kilometre of railway, up to 35t of these waste materials can be reused.
These sustainable sleepers are also able to integrate small solar panels, which would make the railway itself an active accumulator of solar energy (the Greenrail Solar programme) or a kinetic energy system that would generate electricity from the pressure of trains passing over the tracks (Greenrail Piezo). Meanwhile, Greenrail Linkbox can integrate devices designed to transmit safety and diagnostic data.
This has all been developed despite the fact that when Giovanni De Lisi founded Greenrail in 2012, he was informed by chemistry experts that his dream to create sleepers that slotted neatly into the circular economy was ‘simply impossible’.
Fast forward five years and according to the company’s sustainable development manager Dawid Janik, based on the volume of interest in Greenrail’s sleepers from all corners of the world, they now have the potential to become the industry standard.
Elly Earls caught up with David to find out more.
Elly Earls (EE): What have been some of the biggest milestones and challenges along the Greenrail journey?
Dawid Janik (DJ): The development of Greenrail was never easy – it required a lot of persistence, and even more hard work. One of the first obstacles to overcome was the result of a meeting that the company’s founder Giovanni De Lisi had with two Italian ‘gurus’ of chemistry at the early stage of the Greenrail project.
They told him clearly that his plan to obtain an outer shell made of recycled plastic and rubber was simply impossible. Having some funds and strongly believing in his idea, he conducted laboratory tests at his own expense. After numerous tries, the gurus were proven wrong.
Then in 2013, Greenrail was given a significant boost for its growth. The company received serious interest in buying the sleepers and applying its technology in Brazil. Back then we were not ready yet to meet this demand, but it certainly made Giovanni pursue his dream even harder.
The main challenge that we have to face everyday, however, is the particularity of the railway infrastructure market. It can be described as closed and it is definitely in need of innovation. We strongly believe we can change that, encourage more sustainability and introduce new technologies in the sector.
EE: How important has the funding from the EU’s Horizon 2020 programme been to Greenrail’s development?
The EU’s Horizon 2020 SME Instrument Programme was a significant milestone in the development of Greenrail. The company won both phase one and two of the programme, which required a lot of effort to write winning applications, including all the technical, business, market aspects of our products, and a clear development plan.
Currently, the Greenrail SME Instrument phase two project is still ongoing. In its framework, Greenrail is supported by various respected entities, such as Politecnico di Milano, Fondazione Politecnico di Milano, Politecnico di Torino, IdeaPlast, Ecopneus, CNR Pisa, or Sustainable Development Foundation.
Their wide experience and know-how has accelerated the development of Greenrail sleepers, allowed us to conduct various laboratory tests and analyse their results and proceed with research activities for Greenrail smart products: Solar, LinkBox and Piezo.
Apart from significant financial support, the Horizon 2020 programme has allowed us to establish valuable partnerships and widen our European network of contacts. Trainings, workshops and international events organised by the EU’s institutions have been very helpful in deepening our knowledge and developing useful skills, for instance regarding management or reporting.
EE: Your products are cheaper than standard sleepers. How do you achieve this?
DJ: The ability to recycle 35t of ELTs and recycled plastics per km is not all that Greenrail has to offer. Our sleepers ensure significant technical and economical improvements as well.
Greenrail’s outer shell works as an elastic layer, which reduces the track’s settlement and ballast pulverisation. This results in a significant reduction of maintenance costs, which affect a big part of the budget of companies managing the railways.
The reduction of the frequency of renovation works, the longer lifespan and the reduced need of raw material for the ballast inserts replacement also make Greenrail sleepers more economically sustainable.
EE: What stage are you at now with your Greenrail Solar and Greenrail Piezo products?
DJ: Both solar panels and piezo devices have been submitted to severe tests, which have been successfully passed. In the near future, Greenrail Solar and Greenrail Piezo sleeper prototypes will be produced and installed in the field, for testing purposes on a real scale.
EE: How much interest have you had for these products and what form has this come in?
DJ: The interest in Greenrail sleepers is enormous and comes from all parts of the world. This is because of one of our technology’s main advantages: its tailor-made approach. Greenrail sleepers can be designed according to various international requirements and clients’ individual needs. They can be applied on new railway tracks but also during the process of replacing old, spent sleepers. This is what attracts various entities and makes our products recognisable.
So far, the company has received serious interest from the US, Central and East Asia, and the Middle East. Their form varies – sometimes it is an order for a specific amount of sleepers, other times an invitation to build a pilot test in a country, or an inquiry about our license’s acquisition.
EE: What are your next steps?
DJ: At the moment, Greenrail is in advanced talks with various partners on the international level. Soon, the first agreements for the concession of the license for Greenrail manufacturing plants will be signed and announced, which will officially mark the beginning of company’s commercialisation phase.
But we definitely will not stop here – we will keep up the good work and expand to other markets worldwide. The sky is the limit.
EE: How widely do you hope these products will ultimately be used? How big an impact could this have on bringing down rail emissions, as well as reducing plastic waste?
DJ: The need for a technology like Greenrail’s derives indirectly from the growing urban population. This automatically entails an increase in municipal solid waste (MSW) production, which is actually rising much faster than the rate of urbanisation itself.
Every day the world’s municipal population produces as much as 4.8 million tonnes of MSW – a weight equal to 479 Eiffel Towers. A good part of this waste is plastics and rubber. Following the circular economy directives, we treat waste as resource and use it to manufacture a much better product.