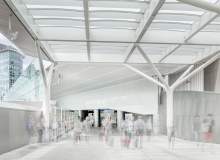
The Paddington Integrated Project (PIP) has been undertaken as a partnership between London Underground, Network Rail, Transport for London and Crossrail to overhaul the layout of Paddington, one of London’s prime rail hubs. Improvements include the upgrade of interchanges between the Underground and mainline trains, better pedestrian and taxi facilities, and a new Hammersmith & City Line station designed by London-based firm Weston Williamson + Partners and built by lead contractor Carillion.
Weston Williamson’s design for the new Paddington Tube station and related interchanges called for bright and airy spaces, making prominent use of stainless steel surfaces, as shown by the columns and wall cladding in the picture above. For the stainless steel elements, the project opted for a sophisticated treatment process to ensure their pristine look could be maintained.
The treatment is called shot-peening, and was chosen following a consultation with shot-peening specialist Wheelabrator Impact Finishers, which also shot-peened steel for the project at its plant in Coventry. The process has previously been used to treat important components in the aerospace and motorsport industries, and it is increasingly employed to create high-spec elements on architectural projects.
Shot-peening involves the hardening of a metal surface by barraging it with thousands of glass, metallic or (in this case) ceramic beads, subtly deforming the surface. The technique makes surfaces hard, scratch-resistant and non-reflective, as well as creating a smart, slightly matte aesthetic.
Among the benefits of shot-peened steel is a much greater resistance to general wear-and-tear and intentional vandalism, an essential trait in a much-used public space that is expected to last for the greater part of the 21st century with minimal maintenance, as Wheelabrator’s business development manager Chris Pallot confirmed. "A surface work-hardened through shot-peening is extremely durable and tougher to scratch – an important attribute in the station’s busy thoroughfares and heavy-traffic pedestrian areas."
The low-reflectivity characteristics of shot-peened steel aren’t just for show; it is also useful to shield drivers alighting at platforms from potentially distracting glare. "We can also fine-tune the reflectivity of the surface within a spectrum from low to medium, striking a balance between getting light into the station and protecting drivers against glare," said Pallot. As a result, elements of shot-peened steel have been incorporated into Paddington’s mainline platform area to improve safety.
The scale of shot-peening required for the PIP created a daunting task for Wheelabrator, which has also carried out shot-peening work for construction projects like Heatherwick Studio in London and the new visitor’s centre at Giant’s Causeway in Northern Ireland. Around 1,500m² of stainless steel was shot-peened and delivered to Paddington between April 2012 and August 2013 when the project was broadly completed, representing 4,000 separate stainless steel pieces of varying size. "The sheer volume of pieces that had to be processed – there was no time to get it wrong," said Pallot.
The end result can be seen in Paddington station surfaces that are built to last. "Applied expertly, shot-peened surfaces do not rust," Pallot commented. "In contrast to some grained or brushed finishes that can produce undercuts which trap moisture and can cause corrosion and rust. For the Paddington Integrated Project we used a very special ceramic bead which has no ferrous residues and is completely sterile as far as carbon contamination is concerned. That means we can eliminate the risk of corrosion and guarantee an immaculate finish for decades to come."
All photos courtesy of Wheelabrator Impact Finishers.