
Since being created to help car manufacturers in the 1950s, fatigue management software has developed from being an in-house pet project to a viable commercial product. These days, many large companies in transport, aerospace and mining use the technology to reduce costs and man-hours when designing new plants and machinery.
“Fatigue used to be the black art that produced financial black holes,” says Professor John Draper, chairman of Safe Technology and author of Modern Metal Fatigue Analysis. “Potential errors were hidden behind the euphemism of ‘safety factors’. And manufacturers paid the price for overweight components that cracked prematurely, a seemingly endless series of prototype developments, unpredictable warranty claims and loss of customer confidence. Traditionally, fatigue failures have been fixed by over-design. But increasingly, engineers are under pressure to ‘design down’ to save weight and material costs. Over-design is no longer a viable option and the need for sophisticated fatigue analysis tools has become increasingly apparent.”
Fatigue analysis software can help reduce development times by making designs correct before a component is cut, according to Professor Phil Irving, head of the Damage Tolerance Group at the UK’s Cranfield University.
“It can make the difference between doing a dozen fatigue tests and one or two, which saves a lot of time and money during development,” he explains. “In the aerospace industry, certain regulations require testing and analysis of fatigue liability in sections of the aircraft. Fatigue software allows you to demonstrate analysis in that instance and it also helps to calculate life extensions for big structures like oilrigs. If you have good information you can recalculate fatigue life and extend the life of your assets. We’re seeing a lot of that in the North Sea at the moment.”
How the software works
There are three major inputs to fatigue analysis software: component load measurements, stress analysis of the structure and material fatigue properties.
How well do you really know your competitors?
Access the most comprehensive Company Profiles on the market, powered by GlobalData. Save hours of research. Gain competitive edge.
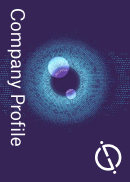
Thank you!
Your download email will arrive shortly
Not ready to buy yet? Download a free sample
We are confident about the unique quality of our Company Profiles. However, we want you to make the most beneficial decision for your business, so we offer a free sample that you can download by submitting the below form
By GlobalData“The software interfaces directly to finite element analysis software and is supplied complete with a database of material fatigue properties to which users can add their own data,” says Draper. “It calculates where and when fatigue cracks will occur – the fatigue hot-spots – plus the factors of safety on working stresses for rapid optimisation and the probability of survival at different service lives, otherwise known as the ‘warranty claim’ curve. The results are presented as contour plots of fatigue lives, stress safety factors and probabilities of failure and plotted using standard FEA viewers and graphics software.”
Dumper barrel analysis
As a global supplier of handling solutions equipment for a range of industries, Metso Minerals turned to finite element analysis (FEA) software to evaluate the design of its railcar dumper barrels.
By designing dumper barrels with FEA software, Metso Minerals engineers were allowed to evaluate high-stress areas prior to manufacturing and ensure the vehicles had a maximum fatigue life span. Three separate design projects were carried out to evaluate the stress and displacement levels at different operational positions and conditions. The software was also used to evaluate the natural frequencies of the main structure.
A 3D structural analysis was carried out that used shell, brick and beam elements to create an image of the dumper barrel and the car geometry. Beam and link elements were also added to represent the clamp system, rollers and support framework. A concentrated mass element representing coal was used at the appropriate locations to evaluate the tip angle and load-case.
The different components of the dumper barrels assembly were connected using ANSYS contact elements and beam elements. For the purpose of the design evaluation, all materials were presumed to behave elastically and homogeneously.
In total, 22 load cases were analysed with 12 different orientations of the dumper car. These were used to compare the natural frequencies of the motor and a full load-case to simulate the effect of having a complete load in the car at different orientations.
The result was a detailed map of the stresses and displacements of the main dumper barrel structure for each load case. Metso Minerals also requested equivalent stress, principal stresses, normal and shear stress, and displacements in the three global directions as well as fatigue and weld assessments.
Advancements and innovations
For years fatigue development software has been unable to cope with one of engineering’s most difficult areas: multiaxial states of stress. However, developers such as nCode and Safe Technology have made huge advancements in this area since 2006.
“Fatigue analysis software research is in an exciting phase,” says Draper. “The last two to three years have seen a lot of the gaps in our knowledge filled in. We are now able to operate without making too many approximations and have software capable of taking into account things like multiaxial states of stress, so the results are much truer.”
Acquiring the information to feed into fatigue analysis software packages can be a costly business. Measuring load components and conducting stress analysis involves employing teams of people, keeping the subject operational and installing systems to conduct trials, which can run into thousands of pounds. Because of this, the data is not always as good as it should be, which can affect the accuracy of the fatigue life predictions.
“Fatigue analysis software is not always wonderfully accurate,” says Irving. “People get around this by inputting data for different materials or reducing the level of stress to get the optimum calculated fatigue life. This life can then be calibrated against an experimentally measured life. The effects of changes in material or stress can be accurately assessed; but absolute fatigue life can be difficult to calculate accurately.”
Irving and his team conducted an experiment once where 12 organisations were asked to use their fatigue analysis software to calculate the fatigue life of a sample component on a helicopter.
“We then did an experimental measurement to find the correct answer, which was 400 flight hours,” explains Irving. “While some of the companies were within a few hours, some suggested the fatigue life should be 250 hours and one said it was 12,000.”
However, Draper believes that the advancements in research over the last couple of years mean that the accuracy of fatigue analysis software is on a par with anything else in engineering.
“We can estimate what an allowable stress is to an accuracy of within 5% now,” he says. “That puts us on a par with anything else in the field.”
Market outlook
Leading IT researcher Gartner expects software spending to increase by 1.5% in 2010. However, the picture for the niche fatigue analysis software market looks far rosier, according to Draper.
“It’s very difficult to put a figure on it, but I’d say this market is growing by about 30% each year,” he says. “I think this kind of growth will continue into the future as more companies and more industries are being forced into reducing costs. The high cost of raw materials means you can’t just throw metal at problems like fatigue anymore.”
Although acknowledging that cost of procuring information to feed into the software may prevent some companies from using it, Irving also predicts a bright future for the market.
“Fatigue analysis software will become more widely adopted as it becomes further integrated with CAD packages,” he says. “I think there needs to be more transparency and a set of standards introduced, so there is more uniformity on fatigue life predictions. But ultimately, as a service experience, I expect the market will grow and the software will become more accurate as time progresses.”