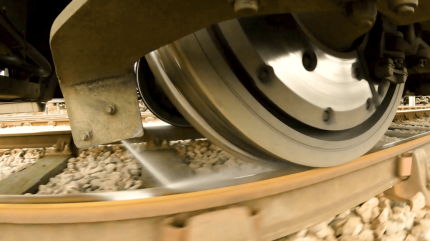
The issue of low wheel/rail adhesion has been a global problem since the earliest days of the railways. Making it harder for trains to accelerate and brake efficiently, low adhesion can result in station overruns, signals passed at danger (SPADs), buffer stop collisions, and train collisions and derailments. The 2023 leaf fall season, for example, had 337,700 associated delay minutes.
Coming to a head every autumn (The most recent figures – from 2019 – cite estimated costs to industry and wider society during this season to be in the region of £355m a year), the issue is often blamed on leaves on the track, but crushed wet leaf film isn’t the only culprit.
You can’t it’s one of the major causes, but low adhesion can also be caused by water, iron oxide, industrial contaminants or a combination thereof. This means it’s a concern to the industry all year round, especially since these contaminants have the potential to electrically insulate a train’s wheels from the rail, failing to short a track circuit and giving the appearance that no train is present.
“These incidents are referred to as wrong side track circuit failures (WSTCFs), which compromise system integrity and could result in a train collision or derailment,” says Ben Altman, senior research analyst at the Rail Safety and Standard Board (RSSB).
Double variable rate sanders
A number of solutions have been developed to tackle this problem over the years, and one of the most promising in Great Britain is double variable rate sanders (DVRS).
Most trains on the Great Britain mainline are already fitted with sanders that discharge a fixed rate of sand, but testing by RSSB found that using two variable rate sanders in series could half stopping distances on a four-car train travelling at 55mph compared to a single fixed rate sander.
RSSB has since supported the Rail Delivery Group’s business case for national fitment of variable rate sanders, which has led to the retrofit of DVRS to Northern Trains Class 323 fleet, South Western Railway fitting its entire Class 158 and 159 fleets with single variable rate sanders and most recently ScotRail beginning the fitment of DVRS on its Class 170 fleet.
“Enhanced sanding delivers variable rates of sand in a speed-dependent manner, meaning sand delivery is optimised at both high and low speeds. This is one of the biggest game changers and it’s certainly something operators should consider investing in,” notes Altman.

Similarly, Arriva Rail London is continuing with its hygroscopic sand trial in partnership with Network Rail.
Hygroscopic sand is designed to absorb moisture and increase friction for more effective braking, and Arriva has been trialling this on its Liberty Line – the Romford to Upminster Overground line.
“We chose the Liberty Line as it’s isolated from other service routes and a known poor adhesion route,” says Terry Ingman, Class 710 Fleet Manager at Arriva Rail London.
“As a trial solution, Network Rail employed additional hand sanding teams to apply the hygroscopic sand along the route. This has now been applied for three years, which means that this year will be a control year to compare data to see if there have been any changes in adhesion compared to the trial years.”
Researching new technologies
Research on other potential solutions continues in earnest, both in Great Britain and overseas. Work has included trials of laser railhead cleaning in the US for example, and high-velocity ceramic particle jets in Japan.
A lot of the work in Great Britain is undertaken and supported by members of the cross-industry Adhesion Research Group.
As the facilitator of this group, the RSSB has been involved in many projects, including testing conductive traction-enhancing particles and examining the early feasibility of using available enzyme treatments to degrade leaf film.
Technologies in development include PlasmaTrack and the Water-Trak system. The former uses a plasma jet of high-energy electrons and ions to thermally remove contaminants, while the latter, which underwent trials by Northern Trains over recent autumns, works by applying small amounts of water from the train onto the rail head, creating rainy-day conditions that enable the wheels to glide safely along the track.
Cryogrip
Cryogrip is another promising solution, which has been developed at the University of Sheffield and trialled on railhead treatment trains. An AI camera fitted to the train monitors the track for areas containing contaminants, and when identified, an underslung cryogenic unit then shoots dry ice pellets that cause the contaminants to crack and break away.
“They essentially come out at supersonic speed, so you get cleaning from the kinetic energy of the very cold (-73o) particles hitting the surface and then the blast from the CO2 turning back to gas,” explains Roger Lewis, professor at the School of Mechanical, Aerospace and Civil Engineering.
There were originally concerns regarding its sustainability credentials, but the CO2 used is not being manufactured, but rather an industrial by-product captured from bio-ethanol production.
“Using AI to identify the area of concern also minimises the number of pellets we have to use,” notes Paul Ferriday, managing director of Cryo Technologies. “If anything, it’s potentially a more environmentally-friendly solution than traditional water-based methods because it uses less energy and resources.”

Trials on Scotland’s Highland line, with a system on a Nexus railhead treatment train, “massively reduced their delay minutes” according to Lewis, and now his team are working with Network Rail and Northern Trains on a proof of concept for use on passenger trains.
Taking this a step further, a proof-of-concept RSSB-funded project is also underway by the University of Sheffield to show how AI can be used to estimate low adhesion on a track. Using data gathered from sensors and the train-mounted camera, the AI model can predict adhesion and provide output in the form of an adhesion probability.
More than 600 data points were collected from six different sites over the autumn and winter of 2019 and 2020 to train the tool and currently, the researchers are inviting industry partners to capture and upload their own data to the prototype tool for long-term analysis.
Industry putting on the breaks?
But while there’s exciting innovation happening around this issue, Lewis points to challenges with the industry accepting and implementing them operationally.
He says he’s often beset by bureaucratic issues and the industry’s aversion to change, while Altman points to the fragmented structure of the industry making it challenging for some organisations to invest in technologies.
“This is because the benefits and costs often don’t sit with the same organisation,” Altman notes.
“As a result, a number of initiatives have been funded through cross-industry investment schemes,” he says, adding that he believes positive changes are planned for the industry in the form of Great British Railways.