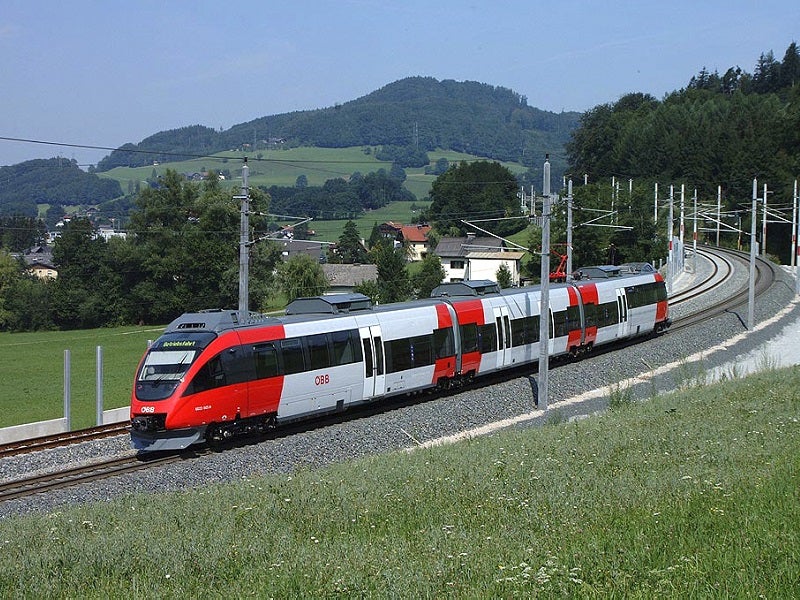
It’s no secret that the railway industry has been increasingly prioritising sustainability. As it stands, around 0.3% of global CO2 emissions come from railways, according to the International Energy Agency (IEA) making it the most energy-efficient mode of transport compared to air and road. Still, railway engineering companies are continually developing technologies to make the industry more environmentally friendly.
One such company is rail equipment firm Bombardier Transportation, which has a track record of providing the railway industry with propulsion systems since 1891. Its first traction converters with power semiconductors were introduced in the 1970s and they have continuously evolved since then.
Specifically, the company’s MITRAC propulsion system – launched in the mid-1990’s – was developed to help the railway industry increase energy efficiency as well as reduce lifecycle costs. The MITRAC system is designed to help repurpose braking energy expended by trains so it can be used during acceleration or autonomous operation of the vehicle.
“The MITRAC system stands for Modular Integrated Traction System and was originally launched to cover control electronics, traction converters and drives,” says Bombardier Transportation head of external communications and public affairs Eric Prud’Homme.
How does the propulsion system work?
Deemed as the “heart, muscles and brain of the train” by the company, the MITRAC propulsion system witnessed an upgrade with respect to its technology in June 2019. The new line of Bombardier’s MITRAC products consists of three segments.
Products in the MITRAC Power portfolio include pantograph and shoe gears for power pickup, high voltage equipment, traction and auxiliary converters, drives, overall braking system and propulsion control.
Its new generation of converters come in two varieties – air-cooled and water-cooled traction converters – and are distinguished in terms of distributed propulsion systems. As Prud’Homme explains, the air-cooled traction converters are ideally suited for decentralised propulsion systems for trains with distributed propulsion such as trams, automated people movers, metros, regional and intercity trains.
The water-cooled traction converters are made to deliver higher traction power and are suitable for mainline trains with centralised propulsion, such as locomotives, and high-speed powerheads.
Secondly, the MITRAC Pulse range of products increase energy efficiency by adding alternative energy storage solutions such as lithium-ion traction batteries and supercapacitors and managing the energy flow, Prud’Homme continues. Currently, the MITRAC Pulse traction battery is under development which he claims “would increase the energy density by 30% therefore increasing the catenary-free operation range of Bombardier vehicles”.
Lastly, the MITRAC Control segment encompasses the Train Control and Management System (TCMS) portfolio, which includes processing units, distributed input and output devices, high bandwidth communication devices inside the train and between train and wayside and driver desk displays.
How has the technology evolved over the years?
Highlighting the changes made to the existing system of the MITRAC Power range, Prud’Homme details that the converters are now “designed and prepared to be future-proof, i.e. easy integration of next-generation semiconductors, especially silicon carbide”.
“The resulting increased and scalable performance density of the converters is then used to optimise other key components such as traction motor and transformer design to reduce the size, noise, weight and losses,” he adds. “This system-level optimisation is further bolstered by the advanced propulsion control methods of the MITRAC EOS control system.”
The upgrade in the MITRAC Control range saw the “introduction of Gigabit Ethernet” to enable real-time data sharing, says Prud’Homme.
These new systems have already been tested on tracks. For instance, the MITRAC Pulse traction battery was trialled in Bombardier’s new TALENT 3 battery train, and the MITRAC Power 1500 traction converter prototype with silicon carbide semiconductors was used in a MOVIA C20 metro vehicle in Stockholm.
Changing times call for better security
While the new MITRAC systems were made to help train companies achieve sustainability, Prud’Homme details that there was a slew of roadblocks during the redevelopment. For starters, the company had to ensure it was digitally protected.
“New challenges for the control systems include higher requirements on safety and increased focus on cybersecurity, i.e. protecting the whole electronics from unauthorised intentional access and manipulations,” he says.
Furthermore, challenges for the MITRAC Control system included “integrating high-bandwidth applications such as passenger information, passenger safety and security systems such as surveillance cameras,” he adds.
Despite the teething problems, Prud’Homme is bullish about the future prospects of the technology. He concludes that Bombardier will continue to focus on “energy efficiency, high modularity, scalability and flexibility, as well as a positive environmental footprint”.