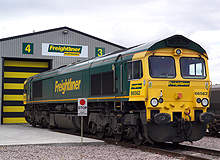
Any organisation running machinery needs to plan for routine maintenance and deal with unforeseen breakdowns, and so they have a supply chain for spare parts and materials. However, running a railway is a bit more complicated than most manufacturing companies; the infrastructure can extend over hundreds of miles and the ‘machinery’ keeps moving about. Add to that the problems of breakdowns in remote locations, public safety issues and penalty clauses for late running and disruption to the network and it’s obvious that getting maintenance right is a key issue.
Trains rarely suffer a complete and unexpected breakdown, much more commonly, small faults develop that do not compromise safety or prevent the train meeting its schedule, but if left unfixed for too long may precipitate a breakdown. A passenger train with six powered bogies can run around for days with an intermittent fault in one of them, and it can keep to time running on the power of five bogies. But if another fails there will be problems. The fault needs fixing soon, but it isn’t essential to pull the train out of service immediately.
The traditional method of dealing with non-critical failures is for the driver to leave a written comment for the maintenance engineers to read when the train is next in a depot, which works most of the time. But if on investigation the engineers decide the fault needs immediate attention they then have to go through the business of creating work orders, and raising purchase orders for parts or service kits.
Wouldn’t it be better if the maintenance team knew of the issue as soon as the driver did, or even before? If they could track the issue, watch it develop, compare it with similar issues in the past, decide when to fix it, where to fix it and make sure all the right parts and materials were in the depot waiting for the train to arrive? That is the reasoning behind Alstom’s TrainTracer system.
TrainTracer
A TrainTracer module added to the train’s control system monitors changes in its major components and reports via radio transmission to a ground-based server. Engineers can remotely analyse and understand what’s happening on board, anticipate any problems or troubleshoot failures.
In the UK, Alstom has used TrainTracer since 2006 on the West Coast Pendolino fleet, which it runs on behalf of Virgin. This technology can be specified on new trains, or retrofitted to existing stock, and they don’t have to be Alstom-built trains.
There are variations of TrainTracer available to suit the operating conditions in different countries, it is used on SNCF class BB46000 freight locos in France and a modified form without the remote communications in China.
It has been fitted to the Class 456 EMU fleet operated by Southern, the Class 319 EMU fleet operated by First Capital Connect, and the Northern line fleet on the London Underground.
We spoke to Richard Close, Engineering Commercial Manager and Lee Gaulton, procurement manager of First Group about TrainTracer on the 319 fleet. They describe it as a system under development, which is already proving useful. First Group is also starting to work with Alstom to implement TrainTracer on its fleet of class 377 Electrostar units, but the majority of the FirstGroup trains are described as ‘mid-life’ stock inherited from previous franchise operators, installing TrainTracer isn’t really an option.
Maintenance management software
DeltaRail XV
First Group’s maintenance scheduling is carried out using TACT from Delta Rail, and the latest enhancement ‘XV’.
XV is the UK’s leading railway maintenance management product enabling depots to maintain what they need to, when they need to, rather than adhering to a set maintenance schedule.
XV reduces costs by increasing the efficiency of data input and management, defects can be tracked, categorised and analysed, allowing engineers to target work that will have the greatest impact on reliability.
First Group’s Close and Gaulton find that the data history accumulated by TACT/XV not only enables them to plan maintenance efficiently, it also helps deal with unforeseen issues.
No-one can predict exactly when things like windscreens will be damaged, but by reviewing the history it is possible to see how many on average are replaced each year, and thus set an appropriate stock level.
Many European train operating companies use XV but another popular choice is Ramsys.
Ramsys
Like TACT/XV, Ramsys is a means of organising all the data coming into an engineering department to facilitate rational decisions. The major difference is that it’s not limited to rolling stock. Any component of a railway, down to individual line welds, can be accommodated in the Ramsys data structure. Obviously this makes a lot of sense when a railway company owns the infrastructure and rolling stock as well as running the trains. However, it is less suitable for the UK with its fragmented rail industry structure.
The diagram above shows the basic structure of Ramsys. It is built in modular form so that operators can add the modules they need without having to buy into the whole package. Mermec claim Ramsys is compatible with standard ERP systems.
Any organisation system is only as good as the data going into it and Ramsys is able to collect data from a wide range of systems and databases, including presumably, data from TrainTracer, though we’ve no evidence the two have been linked anywhere yet.
Spear
Freightliner Group runs 1,800 freight trains a week, pulled by 137 class 66 locos and 6 class 70s. They have another 24 class 70s on order. Dave Reilly, Senior T&RS Engineer, explained that all their locos are equipped with an On Train Monitoring Recorder (OTMR) but the age of the vehicle dictates the level of complexity. A class 86 OTMR covers the basics such as AWS/Vigilance/Power/Brake demand, whereas a class 70 has remote diagnostics that can predict a fault before it occurs.
Freightliner uses a bespoke transport-based asset management system called Spear to plan maintenance. Spear Technologies Inc, acquired by Hansen Information Technologies in April 2006, produces Spear 4i, which is designed specifically for commuter and freight rail fleets, facilities and permanent way maintenance. Dave Reilly describes Spear as “…light years ahead of any legacy systems in use by BR”.
Rather than leave notes in a book, drivers report faults using SPEAR so that when the loco is delivered for repair or maintenance the engineer will look at a terminal and see the complete service history.
Service orders
Whatever monitoring and maintenance scheduling system is used there comes a point when service orders need to be created. Parts not held in stock need ordering, and parts taken from stock need replenishing. In common with many companies in all manner of industries many rail operators use SAP Enterprise Resource Planning (ERP) to run their business functions, including generating service and purchase orders.
We talked to Kevin Prendergast, senior project engineer at Alstom about linking TrainTracer and SAP so that service orders are generated direct from TrainTracer. He said that at the moment it doesn’t happen, but there is a ‘read only’ link. The engineers still have to create orders manually in SAP, but a button on the TrainTracer screen opens a SAP client window, which shows what orders have been made regarding the work to be carried out on a particular train.
Future trends
Directly linking train tracing, maintenance scheduling and ordering of parts is still some way off, but the way things are going it seems the next logical step. Supermarkets already link point-of-sale data to the supply chain, many manufacturing companies do the same sort of thing. Bringing similar technology to railway maintenance is long overdue.
Angel Trains & Southeastern announced on June 24th that they have awarded Alstom a contract for the design, supply and installation of a Traintracer remote condition monitoring system for 93 Networker Electric Multiple Units, built in the 1990s.