
This problem is essentially the same as that caused by adverse weather conditions like snow and rain, which is a loss of adhesion affecting contact between the train’s wheels and the track.
Know colloquially in the UK as ‘leaves on the line’, this autumnal plague on the network costs the rail industry tens of millions of pounds a year for track and train management and results in timetabling delays for passengers.
The frequency of these conditions, and the standard practise of acting only when a problem is detected, means real-time surveillance and quick action is essential. Thankfully a breakthrough system developed at the UK’s Salford University and based on minute scrutiny of wheel and line behaviour may just hold the key to a truly preventative solution.
Age-old adhesion issues
There are several ways the industry currently manages the effects of adhesion issues. Some train companies, such as South West Trains, produce a special ‘leaf fall’ timetable as trains have difficulty accelerating and have to approach stations more slowly, meaning they cannot operate to their normal schedule.
By using equipment such as high pressure jets and ‘smart sanders’, which detect wheel slips and automatically release sand, rail companies can work at keeping the line clear of leaves. Wheel slip / slide protection (WSP) technologies are used, but do not give instant data to the drivers, and as these systems are activated only to stop wheel slip / slide when triggered by sensors, they only offer a reactive response.
"The problem comes when you have certain kind of contamination: water, grease, snow, winter leaves, and you don’t have enough adhesion to deliver traction force or breaking force," said Professor T X Mei, director of CASE Control and the Systems Engineering Research Centre, who has been developing a new preventative approach, in the form of a monitoring solution, over the last four years at Salford University.
How well do you really know your competitors?
Access the most comprehensive Company Profiles on the market, powered by GlobalData. Save hours of research. Gain competitive edge.
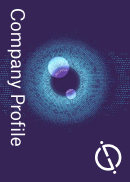
Thank you!
Your download email will arrive shortly
Not ready to buy yet? Download a free sample
We are confident about the unique quality of our Company Profiles. However, we want you to make the most beneficial decision for your business, so we offer a free sample that you can download by submitting the below form
By GlobalData"This has been a problem since the start of the railway and it’s very difficult to manage as there are a lot of uncertainties that make it difficult to tell where this is going to happen."
A new method for monitoring adhesion
The original idea for Professor Mei’s new approach to monitor adhesion conditions came from a previous research project about eight years ago, explained Mei, where they realised that if they could detect changes in the dynamic behaviour of a wheel set, then they could detect the conditions of the track.
According to Mei there are two areas where the observation of wheel-rail contact conditions is difficult. "One is that the adhesion forces have nonlinear features in relation to the relative motion of the two surfaces at the wheel-rail contact points, known as ‘creep’," explained Mei.
"The second is that this non-linear relation is not fixed and can vary substantially and quickly from one section of the track to another. In poor contact conditions the maximum adhesion available can be far below what is needed for the normal provision of traction or braking."
The fact that dynamic behaviour of a train is affected by nonlinearity, as well as the variations in creep characteristics, formed the foundations of the Salford team’s research. For example, where the creep is minimal it can cause a damping effect to the bogies – which is a useful stabiliser – however when the creep is beyond the point of maximum adhesion the forces can have a destabilising effect and cause the wheels to slip or slide, along with other mechanical problems.
Model behaviour
"If you are driving a car in snowy conditions, your wheels spin, and you know that even though you don’t see the wheel, because it is based on your feelings about the movement of the car," said Mei. "So we combined this idea with observations from the previous project and came up with a multimodel approach."
The technology the team has developed uses mathematical models (or estimators) of a train to mimic dynamic behaviours in response to a range of track conditions.
"Once you have these you can use the output of the models to compare with the real output to see which models match the real measurements best," said Mei. "The likelihood is that one or two of the models will match more closely than others because the models are tuned to those particular conditions – and that really is the basis of the whole project."
Standard sensors
Sensors used to monitor the adhesion conditions in real-time are mounted on the bogie of a rail vehicle. They are low cost and familiar to the rail industry, which are two huge advantages for the railway industry.
"Because we are measuring vibrations, the kind of sensors we are using are accelerometers and gyros," said Mei.
"These kinds of sensors are used for tilting trains and for monitoring train conditions and are standard devices that the industry uses."
The driver will receive real-time information based on a series of bands as a result of the output from the system. "It will advise the driver on the track condition and the optimal way to drive the train," said Mei.
"We use bands because this kind of information can never be 100% precise as there are a lot of uncertainties, noise and problems in the system, so you can get a good idea of the level of adhesion this way, but no system could ever get an entirely precise result."
Partnerships for the future
Having put the scientific foundations in place for this new adhesion detection system, the team are now looking for a rail industry partner so that it can be tested and undergo trials. The Salford team have been approached by several different companies and are in discussions to decide how best to move the project forward.
Industry could benefit greatly from the widespread commercial roll out of this system. Rail schedules could be optimised as operators would have knowledge of track conditions in real-time, the associated damages and costs associated with wheel slip would be eradicated, and rail companies would be greener as a result of reduced carbon emissions and fuel consumption.