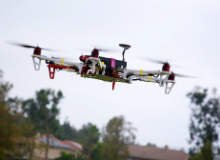
It is often said that the reason around 60% of Americans don’t have a passport is because they can experience the best of many worlds within their own borders.
If a person is in no rush, they could hop on a train in Chicago that takes them through the plains of Nebraska, over the mountains of Colorado and Utah, down into the deserts of Nevada and finally to California and the clear blue of the Pacific Ocean. Covering 233,000 miles, the US rail network connects towns and cities of all sizes, crossing every kind of terrain and climate.
Such a large, varied network throws up a host of challenges as well as advantages. Maintenance is a massive ongoing task, particularly with large areas of track lying hundreds of miles from the nearest town. Track should ideally be inspected by foot on at least a weekly basis, especially in areas of the country prone to extreme temperatures, making maintenance a labour-intensive and expensive process.
Unmanned power
The idea of using unmanned aerial vehicles (drones) to help with this process has gained traction in recent years. In 2013, for example, German state railway operator Deutsche Bahn started using drones to combat graffiti artists, whose work was costing €6.7m a year to remove. Now, realising the potential of the technology for use in the remote corners of its network, US rail operators are making the move into unmanned territory.
In October 2015, the US Federal Aviation Administration (FAA), Boeing-owned drone manufacturer Insitu and BNSF Railway, the second-largest freight railway network in the US with 32,500 miles of track, used a ScanEagle UAS drone to take real-time video and stills of 140 miles of track near Vaughn, New Mexico. Not only was this the largest drone operation to take place in the railway industry, it was the first FAA-approved beyond-visual-line-of-sight operation to be carried out with a drone on mainland America (drones have been used by oil companies in parts of Alaska above the Arctic circle).
As well as flying beyond the operator’s line of sight without incident, the team was able to hand over control of the drone to other ground stations along the track, suggesting that the potential distance drones can cover is hindered only by battery life.
“BNSF wanted more information than they could currently collect on their track and they wanted it with some velocity,” says Charlton Evans, Program Manager for Commercial and Civil UAS at Insitu. “They wanted the frequency of how they could measure and do inspections to go up, so that drove them to unmanned systems… This was an effort to see if we would give them the kind of information they were looking for over large areas of track without flying humans over the track. It was pretty groundbreaking as there was nobody in the airplane to see and avoid others flying around.”
Red tape and camera film
From a regulatory standpoint this operation was unprecedented. It took nine months of sometimes tense discussions to ensure that all ground obstacles and airspace were clear while the drone was in operation. The lessons learned from this process have gone into the creation of a formal document drawn up by the FAA, which provides a ready-made framework for future drone deployments. A lot has to happen, however, before drones can be employed at optimum effectiveness and in more built-up parts of the rail network.
The ScanEagle UAS, however, did not use the best available technology. As the mission was about proving rather than refining the concept of using drones for track inspection, the drone was fitted with one of Insitu’s stock cameras. While capable of spotting visible flaws like track erosion and warpage, more sophisticated cameras and sensors are required to pick up the small cracks in rails and spike that railway companies want to be able to see from the air.
To reach the desired level of sophistication, new technology will need to come to market. The Insitu team is currently looking at high-resolution still imagery and cameras that capture imagery in different spectra (beyond the spectrum of vision), which should be better equipped to capture detailed data while moving at high speed. For this technology to be drone-mounted, new developments in the miniaturisation of sensors might first be needed.
Another major challenge relates to collecting, relaying and processing the data that the drone collects. The drone used in New Mexico relays back video in real time, but this is unsuitable when it comes to the kind of in-depth analysis that Insitu intends to do. To this end, in December 2015 Insitu acquired 2d3 Sensing, a technology provider that specialises in using complex algorithms to process motion imagery.
“You couldn’t put enough people in front of monitors to watch the video in real time to see the kind of details they are looking for, so the data storage and analytics are going to happen on the back end,” Evans says. “That’s one of the hurdles the entire industry faces – massive amounts of data come in and sorting it out into the bits and pieces that actually mean anything to anyone is a huge problem.”
No lack of enthusiasm
The willpower certainly seems to exist on the part of the railway companies. The partnership between BNSF and Insitu has been extended beyond last October’s trial and the country’s largest freight network Union Pacific is also exploring the potential of drones, its CEO Jack Koraleski told Bloomberg in 2014. Both parties stress the use of drones as a supplement to existing methods, not a replacement (at least for now).They will be hoping that the technological and legislative pieces fall into place sooner rather than later.
“There’s a core of folks within the FAA who are very interested in making progress and when they partner with folks like us who want to meet them in a low-risk, high-safety way we can get it done,” says Evans.
“There were some difficult moments over those months [of negotiation]! But it was good because everyone walked away with a better understanding of the problems that we have to tackle.”