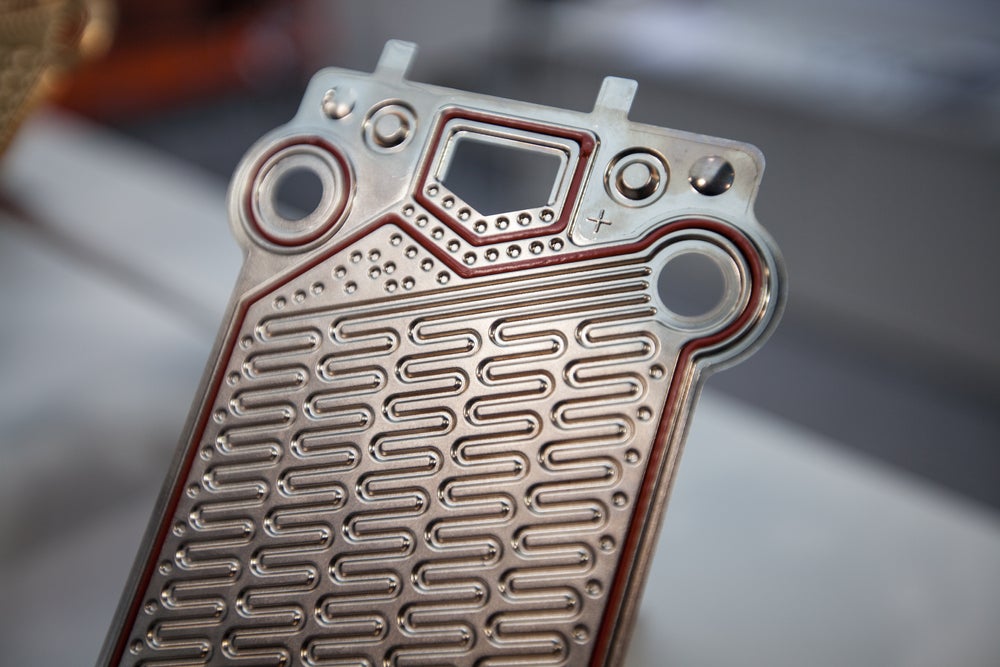
Despite advances in fuel cell technology and an ever-pressing need to reduce our fossil fuel dependency, barriers to hydrogen-powered vehicles remain. From insufficient re-fueling infrastructure to rising hydrogen prices in the US, many challenges face this industry. Regulatory issues also abound, with safety a key focus considering a build-up of hydrogen in the air can cause an explosion at concentrations of just 4%.
To ensure the highest level of safety, leak detection is a critical part of the process but introduces its own set of complications. We spoke to application experts to understand leak detection challenges in FCEV manufacturing and learn about the unique solution Pfeiffer Vacuum has been working on to help the industry combat these.
A lack of helpful guidance
Over a year ago, we published an article on the limitations of leak detection regulations for FCEV manufacturers. It discussed how current standards have restricted the possible methods while not providing any regulations on pass/fail criteria. This lack of helpful guidance is a continued source of frustration for manufacturers.
“All of this slows down the process,” explains Dr Philipp Schurig, market manager for industrial leak testing at Pfeiffer Vacuum. “When you don’t have a rule or standard to follow, you have to do your own research and consult with all the different channels, such as leak detection companies or research institutes. You end up with many different answers and you don’t know which is appropriate.”
Speed over sensitivity?
We don’t have to look too far into history to understand the dangers of hydrogen. But while safety has always been the focus in the hydrogen economy, Dr Rudolf Konwitschny, application specialist at Pfeiffer Vacuum, notes an interesting shift in the FCEV market as companies move towards more function-based specifications where speed becomes the main concern.
“The heart of a fuel cell vehicle consists of a fuel stack, which consists of 250 to 400 individual sequences of bipolar plates for a passenger car and can be in the order of magnitude of 700 layers for a truck or lorry,” says Dr Konwitschny.
“In this case, people are talking about high-volume production. There are many plants being constructed or planned with an annual capacity of around 10 million bipolar plates per year. When you break this down to cycle times, we are in the range of one to three seconds per plate, and some people are talking about making this even shorter.”
With the industry’s current approach to leak detection, this speed is hard to achieve. Bipolar plates have three distribution flow channels that allow the passage of reactants on either side, including channels for hydrogen, air, and cooling. To guarantee the detection of every possible defect in the plate, each channel must be tested in both directions and to the outside. The sum of all channels is then tested to the outside, resulting in a time-consuming routine of ten consecutive tests per bipolar plate.
Time is also a challenge when it comes to production set-up. Many leak detection tools are difficult to adjust to plates of varying heights, lengths and widths. Since downtime for retooling is required between product changes, this inflexibility may be acceptable for research institutes but is inacceptable for serial testing in an industrial production environment.
Interactions with the test medium
According to Dr Konwitschny, FCEV manufacturers are investigating a range of bipolar plate materials, including highly durable carbon-based materials and lightweight metallic alternatives, which might require a coating to improve corrosion resistance. When introducing a new test method, it is important to study any interactions between the test medium and the bipolar plate’s surface. Adsorption and desorption on non-metallic coatings are both key reactions to look out for.
Not only may the process media interact with the bipolar plate materials, but also media used in the testing process. Tracer gas memory effects will generate background noise thus leading to poor gauge repeatability and reproducibility and process capability. Memory effects are heavily influenced by channel material choices. Still, it is possible to minimise these effects through purging steps and a carefully designed test routine.
Fast and flexible – The latest innovation in bipolar plate testing
Pfeiffer Vacuum has more than 60 years of experience in leak detection and is always looking for ways it can solve industry problems through innovative solutions. When a long-term customer from the fuel cells market approached the company to partner on a joint project, Pfeiffer Vacuum’s role as vacuum and leak detection experts was to find the best approach to realise this process step within a high-speed manufacturing line. The outcome was that a brand-new concept was developed and a new bipolar plate leak test module was born.
“With our unique company profile offering all of the measurement instruments, the vacuum pumps, the valves, and the specialists from two of our sites in Germany, we had a unique chance to develop a very versatile leak detection module to fulfil the customer’s R&D needs,” says Dr Schurig, who led the project.
To reduce cycle time dramatically, a novel idea was formulated to keep test cycles to a minimum while guaranteeing safety. “We used combinatorial methods to analyse how many tests are needed in order to have an intelligent, mathematically logical combination,” explains Dr Konwitschny. “We are then not necessarily making the five or six tests individually but grouping them in a way that they can be separated by mathematical analysis.”
Since the module was originally intended for the R&D space, flexibility and versatility were important. The solution included the capability to test one design of bipolar plate with different thicknesses, while further geometries can be tested from the system with a change of inlay. The test cavity can be configured with one or multiple nests for individual or simultaneous tests. In-line testing is also possible for higher volume production, and a modular design means integration into the line is simple, with all product handling managed by the customer.
The new leak test module developed by Pfeiffer Vacuum combines both speed and flexibility. It is easy to integrate and comes from a company with trusted leak detection expertise and a full portfolio of components produced internally.
To learn more about Pfeiffer Vacuum’s approach to developing customized solutions from customer requests, watch the webinar below.