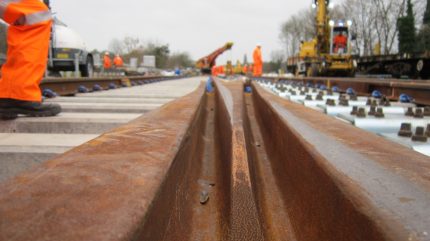
Some of the railway sector’s most important components are made of steel, including gantries, platforms, and overhead signalling systems – even down to the intricate nuts and bolts used to join rails and fasten tracks.
However, due to its innate nature, steel is highly susceptible to corrosion, which is why an appropriate coating must be selected to ensure it can withstand the elements and remain fit for purpose – especially so during the current cost-of-living crisis where businesses are seeking solutions that provide true value for money.
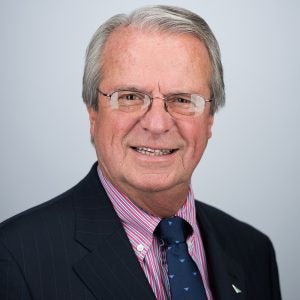
The galvanising industry has partnered with the rail sector for decades – providing a robust, long-lasting, and durable galvanised finish of choice. But some of the rail network is at risk of regressing to ‘the rusty railway’.
The problem with rust
With steel boasting qualities such as being able to withstand immense weight and pressure and endure harsh weather conditions (when finished appropriately), it’s clear why it’s the material of choice for the rail industry. But without a sufficient coating, it’s highly susceptible to corrosion.
And I’m sure it’ll come as no surprise that as a galvaniser, I don’t like rust!
As a veteran in my field, I recall how in the 1960s our rail network was dubbed the ‘rusty railway’ due to its premature corrosion. Paint was typically used to coat rails at the time, due to being both easily accessible and the most affordable (in the short term), but typically only had a lifecycle of around 10 years.
As a result, the components started rusting relatively quickly and began flaking, creating an unappealing appearance that required significant continuous maintenance and was widely mocked – not just in the industry but by the general public too.
Since then, thanks to its abundance of benefits, galvanising has become a prominent choice as a solution for the rail industry.
What is galvanising?
Following its introduction in the mid-1700s, hot-dip galvanising companies have worked closely with the rail sector, supporting projects and businesses worldwide. As a completely unique process, galvanising allows components to be evenly and entirely coated with molten zinc, ensuring a permanent finish is applied, which boasts the greatest resistance to damage.
Galvanising will last for more than 70 years without the need for maintenance or downtime, meaning the overall lifecycle costs remain low – significantly saving time, labour, and resources: particularly important during the current economic climate.
Plus, it caters for even the most eco-conscious customer – galvanising is the original green solution.
In recent years, the rail sector has certainly been in the spotlight. The development and implementation of the UK’s new high-speed rail line is set to form the backbone of our transport network by providing zero-carbon journeys from Birmingham to London.
However, it’s interesting to note the increasing use of weathering steel for bridges throughout the project.
Is weathering steel better?
Over the years, we’ve collaborated with alternative coating companies in completing some of the UK’s biggest projects in this sector, including those that provide weathering steel. Especially when dealing with bigger articles that cannot fit into the galvanising bath, or for projects where the finished item needs to blend into its environment and complement its surroundings, such as woodland.
However, aesthetically, it looks very different to the galvanized steel that customers and the wider public have come to know and love. Instead, it begins to surrender its outer coating and starts to corrode almost immediately, causing it to have a rust-like appearance for its entire lifetime.
To counteract the loss of this surface layer, steel sections are designed oversized from the outset, with the additional metal thickness resulting in as much as 17% more steel being needed. This incurs more costs, more time, and more waste – meaning it’s potentially unsuitable for an entire project.
With HS2 being the biggest infrastructure project of modern times, we in the UK want it to be a resounding success. But as we enter 2024, I’m intrigued to witness further industry changes including how and where weathering steel will be used.
Will HS2 become the ‘new rusty railway’? And will this unusual design choice tarnish the perception and future of steel in general? This is our chance to shine – our time to showcase this exciting project to the world, and to be seen as the true innovators and leaders in this arena.
Personally, I want to ensure that we embrace this wholeheartedly, and collaborate to ensure that the completed project is one we can all be proud of for generations to come. And not a new rusty railway for the 21st century.