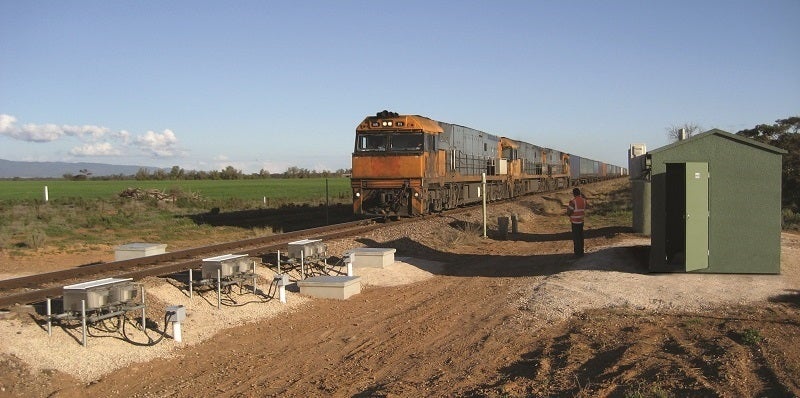
Wayside Inspection Devices (WID) is the developer and supplier of truck bogie optical geometry inspection (TBOGI) wayside monitoring technology.
With over 20 years of industry experience, WID has grown from a groundbreaking pioneer to an industry reference with installations on five continents.
Truck bogie optical geometry inspection solutions for rail vehicles
WID’s TBOGI technology suite provides the railway industry with a unique method of directly measuring the geometry and stability parameters necessary to evaluate the wheel-rail interface, for both bogies and locomotives. Only the full complement of these metrics can reveal when, and how, the wheel-rail interface is compromised. With this information, railways can identify and prioritise the fundamental issues that most need to be addressed.
WID is well-known for supplying systems that are railroad-tough and accurate. The systems carry a low cost of ownership, are easy to maintain, and provide data that is highly repeatable.
WID works with freight, passenger, and heavy-haul railways. Because the TBOGI systems identify and monitor fundamental defects, the systems have a proven history of reducing derailments, service interruptions, wear on the rail, and wear on the wheels and bogies.
Wheelset hunting and geometry measurement solutions
TBOGI wayside systems measure the tracking behaviour (geometry) and tracking stability (hunting) of wheelsets and bogies.
TBOGI systems are wayside technology. Therefore, they need to be installed only at trunk points of a network (on straight track), where the system can watch traffic go by at line speed, or close to it. This makes TBOGI a cost-effective method of capturing the state of all rolling stock and trending it over time to know when, where and why the costliest issues are emerging.
Whether monitoring only a few hundred wagons, or a few hundred thousand, TBOGI systems ensure optimal performance.
TBOGI comes in two forms. TBOGI-TR systems are designed for transit and metro railway environments, including tunnels, elevated guideways, metropolitan areas, or multiple-track main lines. TBOGI-HD systems are designed for the harsh environments of freight and heavy haul railways, including remote, dusty, snowy or extreme temperature locations.
Derailment risk assessment
Railways using TBOGI have noted significant reductions in derailments and in the risk exposure from extreme defects. TBOGI identifies extreme defects that inflict ongoing damage at the wheel-rail interface; many of these are not caught by other condition monitoring systems.
Distinct from other wayside monitoring systems, TBOGI technology is able to assess derailment risk holistically, and with much greater immunity to external factors. The optical-based TBOGI systems measure the full range of wheelset and bogie performance metrics and reflect the true performance, irrespective of variable external factors.
Inspection and maintenance optimisation
TBOGI systems augment maintenance activities and greatly enhance the effectiveness of inspections. During routine inspections, a maintainer can see that a defect has not exceeded a threshold. However, without TBOGI data, the maintainer cannot know how fast the degradation is accelerating or predict the timing of future condemnable measurements.
The trending capabilities of the TBOGI systems allow it to notify maintenance of existing extreme defects with high confidence, as well as notify of defects that are degrading rapidly and will cause future service interruptions if not addressed.
Detection of tracking, angle-of-attack and hunting defects on railways
TBOGI detects defects that cause accelerated rail wear regimes, including:
- Tracking Position defects: inflict head checking and gauge-corner cracking, as well as rail head cracking from shelling and longitudinal fatigue
- Angle-of-Attack defects: inflict intermittent crown wear as lateral material flows, lateral fatigue cracking that can lead to rail breaks, and surface breaking cracks that can develop into rail squats
- Hunting defects: inflict a combination of wear patterns, in particular, repeated flange impacts and scrubbing wear actions against the rail
The above effects on the rail network are usually most pronounced through curves but they can manifest throughout the network, resulting in more grinding and rail replacement. By using TBOGI, railways can significantly reduce these wear regimes throughout their networks.
Rolling stock lifespan improvements
Degenerative bogie performance can be self-feeding. Asymmetrical wear patterns that develop on the wheels both increase stress on bogie components and accelerate the loss (and failure) of material from the wheels and rails. This increase in the wear regime at the wheel-rail interface is measurable with TBOGI.
Railways using TBOGI report significant increases in the lifespan of wheels and other bogie components (including bearings, brakes, and suspension) that are subsequently under much less stress once the defects identified by TBOGI have been addressed.