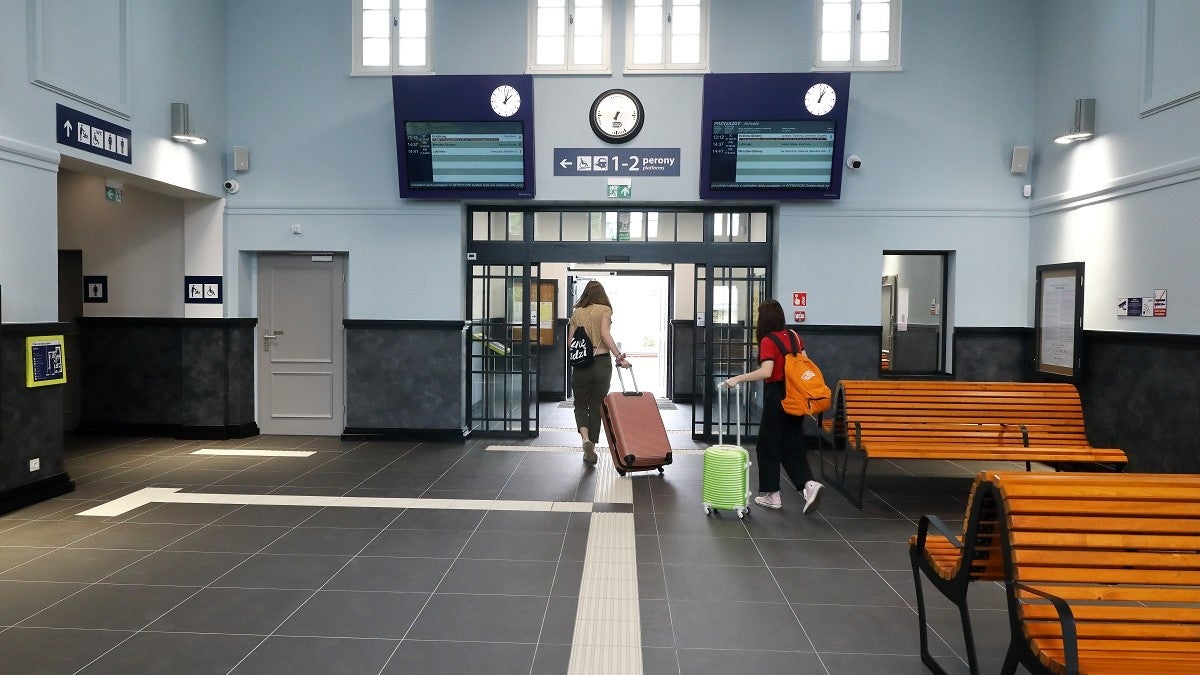
DYSTEN, the dynamically growing manufacturer from Zabrze, has experience in the implementation of passenger information display systems (PIDS), both at passenger stops and at small, medium, and large stations. Another PIDS will soon be launched at the Łódź Kaliska station which, according to the PKP PLK classification, is a premium category facility. As part of the project, the station was equipped with more than 160 dynamic passenger information system (DPIS) devices and a public address system. The company supplied more than 80 pieces of equipment to an equally important regional transport hub in Radom.
Among the architectural gems, the company can boast of having completed a project for the railway station of the Polish State Railways (PKP SA) in Białystok, which won the ‘Building of the Year in the North-Eastern Region of Poland’ competition. The company also became a subcontractor in the implementation of the DPIS for the Warszawa Główna Osobowa station, which began operating trains after 24 years of oblivion. DYSTEN manufactures, supplies, installs, and commissions DPIS equipment for specific sections and stations of railway lines such as E59, 28, 357, 274, or 275.
Cooperation in the implementation of DPIS railway projects with DYSTEN
The manufacturer of DPIS equipment is looking for partners in the foreign market. The PIDS supplier works with the designers, integrators, and subcontractors.
Depending on the customer’s needs, DYSTEN manufactures and supplies a complete DPIS or individual devices of the visual information system, voice information system, time signalling system, or train movement sensors.
The company holds the IRIS certification mark, which confirms that DYSTEN products meet the stringent quality requirements of the international rail industry for activities in the area of passenger information systems.
What is it like working with DYSTEN? This is explained by DYSTEN product delivery department director Barbara Metzner-Moryc, who guided the company through the implementation testing process for railway passenger information equipment.
“Each project is managed by a qualified project manager who is the main point of contact for the client. This enables efficient communication and coordination of activities within our company structure. The manager is actively involved in every area of project delivery, from coordination meetings through installation and commissioning to final acceptance.
We remain available to accommodate client expectations, as well as contractual and site requirements, even if this requires us to work evenings and weekends. We handle each project with personalised attention, which results in the quality and timeliness of the project, as well as a positive relationship with the client.”
TRAKCJA SA, one of the largest companies operating in the rail, tram, and road infrastructure construction sector in Poland, summarised the cooperation with DYSTEN in its reference concerning the supply, installation, and commissioning of the DPIS at the Warszawa Główna station:
“When implementing the agreement, DYSTEN has demonstrated reliability and professionalism certified by its vast knowledge and experience. The agreement was performed on time, and the equipment supplied was made with the utmost care and quality. We therefore recommend DYSTEN as a reliable and trustworthy company, which is very well prepared to cooperate in the supply, installation, and commissioning of dynamic passenger information displays. Experienced staff and technical and organisational capabilities guarantee a high level of cooperation,” stated a reference excerpt from TRAKCJA SA Warsaw from 27 February 2023.
We invite you to discuss cooperation in the field of railway equipment. For more information, please follow the links on our profile.
This year you will find us at our company stand at the TRAKO fair. The largest and most prestigious fair in Poland and the second Europe meeting of the rail transport industry will take place on 19-22 September 2023 in Gdańsk. Come and join us!