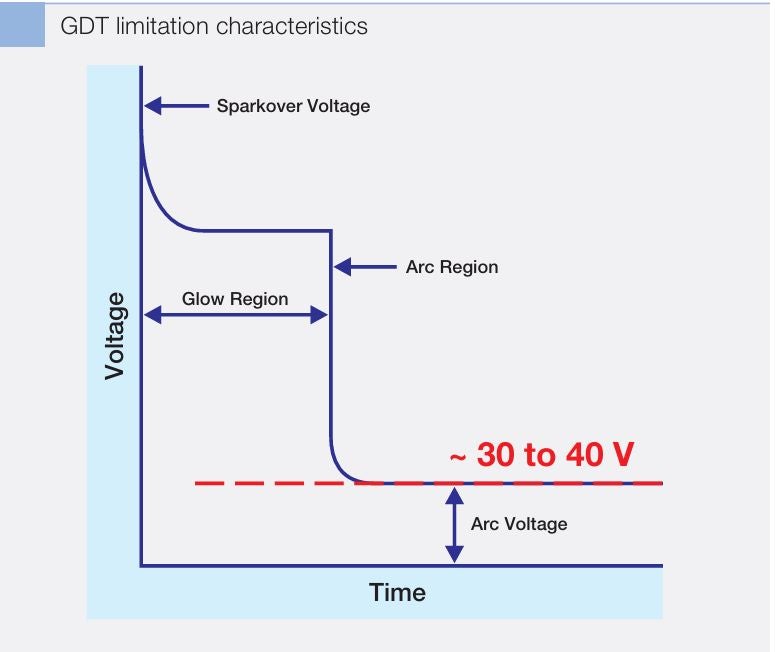
New innovative construction
Based on many years of experience with Voltage Limiting Device (VLD) applications and the requirements of most customers, SALTEK has developed a new, modern VLD class 1, with the possibility of remote indication of the VLD status. The current practice of DC and AC systems uses VLD-F designed on the basis of a gas discharge tube connected to an automatic short-circuiting device which, in the event of a fatal traction fault, always operates in a non-repeatable mode and it goes into a permanently conductive state. This complies with the requirements of EN 50526-2 and other standards. However, if such an event occurs, a permanent short-circuit opens up between the isolated rail and the ground, through which stray currents escape permanently. This permanent current leakage has a very adverse effect on the service life of the metal infrastructure (poles, bridges, waiting shelters, cables, and reinforced concrete structures) alongside the railway track due to electrochemical corrosion caused by the current flow.
Current solutions offer only one way to minimise this damage, consisting of frequent physical inspections of the installed VLD-Fs, which is a challenging task because a reliable verification of the function requires the VLD to be disconnected from the rail, followed by impedance measurements with a sufficiently powerful current source, and then the reconnection of the VLD-F to the rail. This takes quite a lot of time (sometimes around ten minutes) and costs considerable operating money (OPEX), so that the intervals between checks are often extended and the risk of damage to the infrastructure increases disproportionately. The new, patented VLD-F SALTEK solution means revolutionary changes in the use of VLD-F and the elimination of the complications associated with it.
The short-circuiting device inside the new SCG is specially designed and reacts very quickly to the current flowing through the discharge tube. At the moment of its overload or destruction threat, it shunts it out and ensures a permanent short-circuit with minimal energy loss so that there is no physical damage to the product housing that could be dangerous to the environment. This short-circuiting device is wirelessly connected to detection electronics that registers such a change and are capable of permanently indicating it. The electronics consists of a special RFID tag that can be read remotely by a commercially available RFID reader in a fraction of a second, without any manipulation (shunting, disconnecting, measuring) to the VLD. Reading is possible even while moving, making the inspection of the installed VLD-F simple and operationally inexpensive. This allows more frequent VLD inspections and minimises the time when dangerous corrosive current leaks through the activated VLD. Another advantage of this solution is the significantly simpler and more transparent logistics, because in addition to the indication of immediate necessity to replace the VLD-F, other identification parameters of the VLD to be inspected (such as serial number and installation coordinates) are stored in the controller memory, which can then be used as a basis for operational statistics, analyses, etc.
The use of this modern VLD-F therefore results in a significant reduction of operating costs for the management of the railway protective bonding system, as well as a minimisation of stray currents and thus an increase in the lifetime of railway, which also applies to third-party infrastructure. It also results in the possibility of advanced analyses entering predictive maintenance systems for the purpose of inspection optimisation and a further reduction of operating costs. The integrated protection against lightning and industrial short-term pulses integrated into the product and operates in a repeatable mode, where the internal short circuiting device does not react after a lightning strike.
Where I can and cannot apply the SCG?
For many years it has been common practice to install VLD-F anywhere in DC and AC powered railway lines. This installation has often not been associated with infrastructure corrosion problems. With increasing traffic on the lines, changing power infrastructure and train propulsion systems, infrastructure failures appear more and more frequently, along with damages that can be clearly attributed to improperly installed VLD-Fs designed on the basis of gas discharge tubes (GDT). The crux of the problem lies in the combination of the behaviour of GDT at different voltage levels.
This arc features specific voltage parameters- depending on the type of lightning arrester, the arc burning process stabilises the voltage between the GDT terminals (and thus the terminals of the whole product) at a level of around 30V (depending on the arc length). This is the basic principle of GDT voltage limitation, of course, but also the basis of the problem in some applications, specifically there where, for whatever reason, the voltage potential of the track (rail) exceeds the 30V level. The causes of such a condition are varied and often difficult to identify, but result in the fatal destruction of the VLD.
At the moment when the trigger pulse activating the opening of the VLD disappears (it can be a very short pulse of higher voltage, since GDT react within nanoseconds), but when a potentially higher voltage than the burning arc (30 – 40 V) is present simultaneously on the track, then usually the hard source of this potential takes over the role of energy supply of the already burning arc and it burns often for tens or hundreds of seconds. At these voltage and current levels, usually in the order of tens to hundreds of amperes, inevitably result in thermal overload of the GDT and its electrical and mechanical destruction. It also often causes physical destruction or damage to the entire VLD. This can result in the VLD ‘secretly’ become permanently conductive and the problem is only discovered by the next physical inspection and measurement, which often is too late from a corrosion perspective. In such situations, the use of VLD-F Class 1 is highly inappropriate.