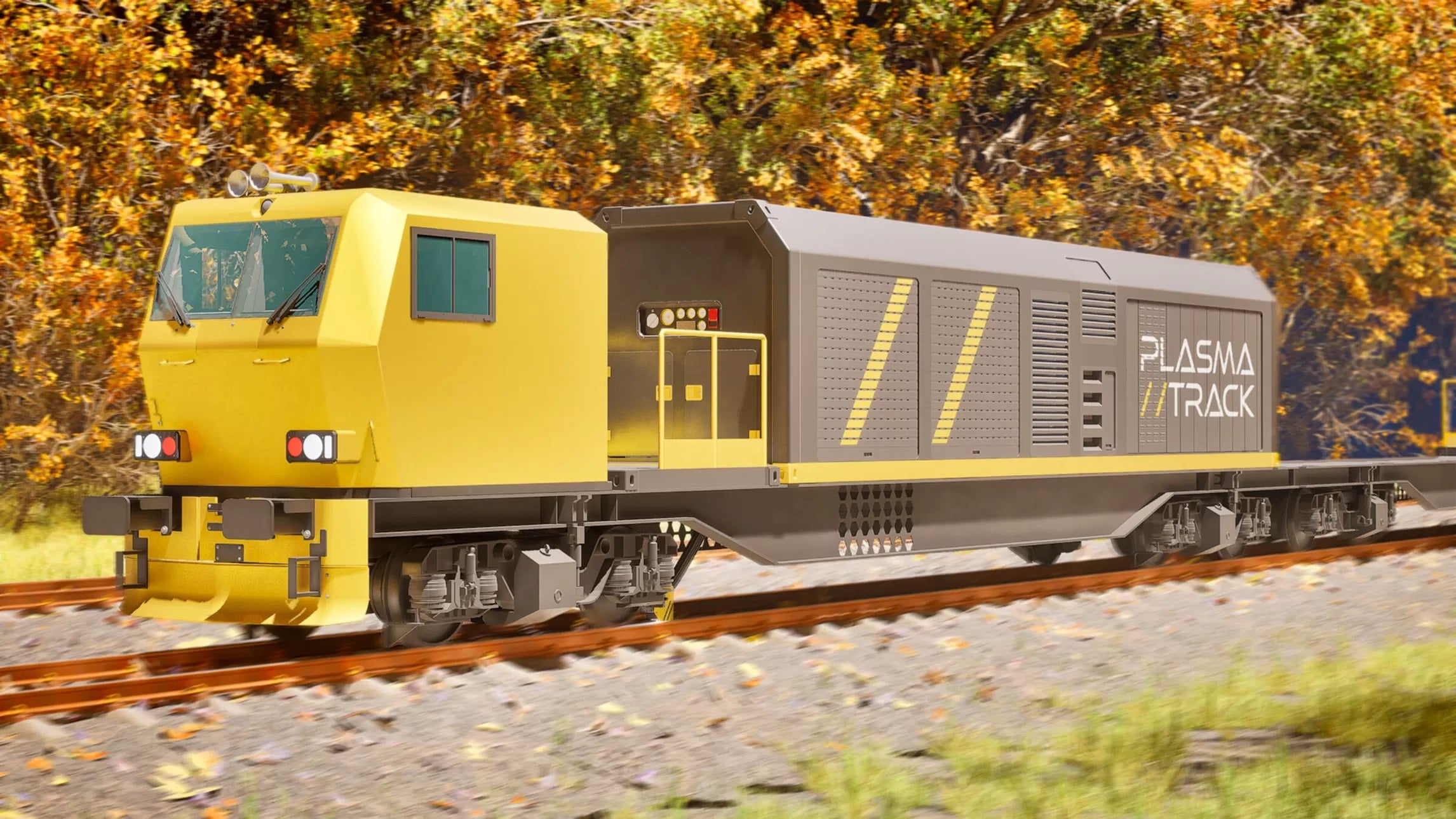
When trains travel over autumn leaves on the tracks, the heat produced by friction between the rails and the tracks, as well as the mass of the train itself, can turn them into a thin, greasy surface layer on the line.
Managing this is an expensive endeavour, with Network Rail’s operation to reduce autumn leaf fall in the UK costing £355m. While the problem has existed since the first railways were constructed, the techniques used to offset the issue have moved at a sluggish rate.
To combat this issue, UK-based startup PlasmaTrack is developing a plasma-based solution, with the aim of providing a commercially viable and sustainable rail cleaning solution.
Cat Vitale speaks to PlasmaTrack CEO, Julian Swan, to find out more about this technology and how the company is planning to advance in the future.
Cat Vitale (CV): When was PlasmaTrack founded?
Julian Swan (JS): PlasmaTrack was founded in March 2020, and it’s actually a spinoff from another business that I run, called The Imagination Factory.
We developed the technology, initially within The Imagination Factory, through UK Government funding, looking for predictable and optimised braking solutions for the railway industry.
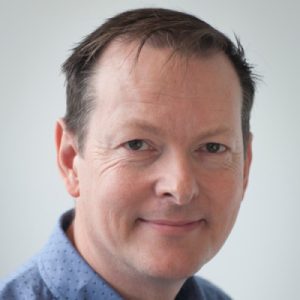
Once we completed that piece of work, the intellectual property and the technology were spun off into PlasmaTrack as a separate entity. At that moment in time, we started working with Network Rail to demonstrate the PlasmaTrack technology as part of their future technology trial on the UK network.
PlasmaTrack has a team of six employees, mostly engineering, and we also work with other specialists in plasma from various UK academic institutions.
Neil Welsh is one of our advisors, and he used to work with Network Rail. He gives us advice, specifically from that stakeholder’s perspective.
Under PlasmaTrack, manufacturing is covered by a subcontract manufacturer that we use, which is called Metallisation. So overall, there are probably about 20 people involved in the design, development, and delivery of our products.
CV: What is PlasmaTrack’s mission in the transport sector?
JS: PlasmaTrack’s plasma-based system is pitched as a seasonal ‘leaves on the line’ problem. However, we believe it is an all-year-round problem, which doesn’t just impact the UK.
The starting point was the UK Government and the Railway Safety and Standards Board (RSSB) calling for rail solutions aimed at predictable and optimised braking with a goal of easing autumnal challenges, allowing us to embark on a feasibility study.
We started off looking at microwaves as a solution to clean the tracks to remove the leaf layer. However, it became very apparent that that wasn’t appropriate in terms of the core technology or robust enough for the railways.
Therefore, we pivoted during that feasibility study from a microwave solution to a plasma solution, and that’s what we’ve been working on ever since.
Our product works by passing a high voltage direct current through a compressed gas – nitrogen – which is easily extracted from the surrounding air. This converts it into a plasma jet of high-energy electrons and ions, which is then delivered to the rail head at speeds of up to 60mph (95km/h) and temperatures of around 700°C.
With a single pass, the plasma jet thermally removes the compacted leaf layer and returns the track to a clean, dry, and uncontaminated state capable of supporting summer braking conditions.
Part of what drives us is the technological answer, but it’s also about changing the way the railway functions, making it more efficient, environmentally friendly, and running at the level it should, where you can rely on it and avoid delays.
We believe we’ve got a technology that can help the rail network with solving terminal challenges. We want there to be preventative cleaning action by the operator.
CV: what problems are you hoping to solve in the rail sector?
JS: Firstly, the main issues we are dealing with are seasonal challenges within the industry, where the leaf layer is produced by the trains themselves, crushing the leaves onto the tracks.
It’s not like you would have a slippery leaf that you stand on; rather, the leaf is compressed under extreme pressure and temperature, creating a hard Teflon-like surface that is more slippery than engine oil when combined with the dew point [the temperature to which air must be cooled to become saturated with water vapour] or a little moisture throughout the year.
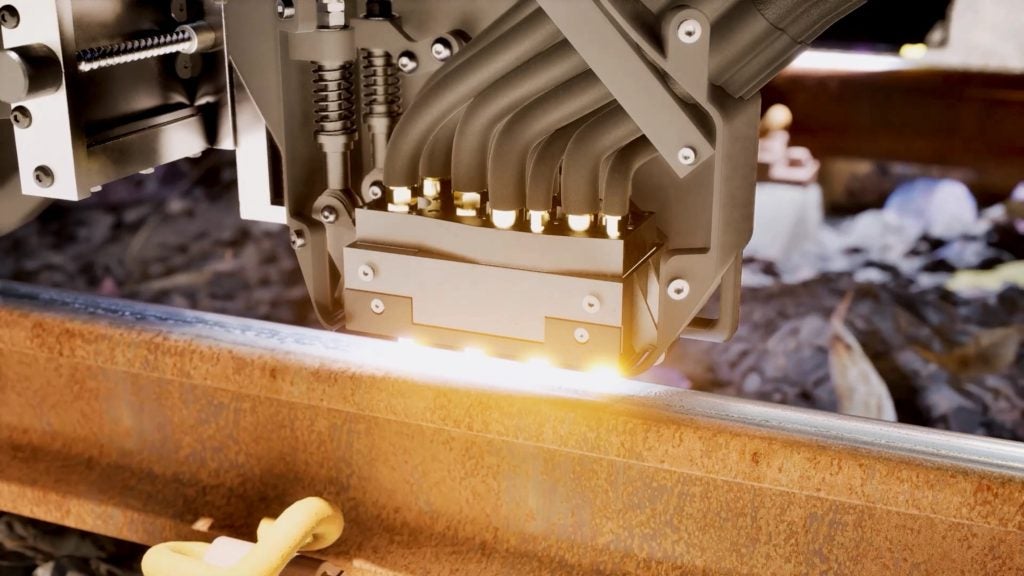
Other pollutants provide further complications. If you have a track that isn’t utilised very often, an oxide layer can form, resulting in a type of corrosion surface. This can cause issues with slip-sliding and adhesion, as well as what is known as a track circuit.
PlasmaTrack aspires for trains to function as if they are on a clean, dry track with certain breaking conditions all year, which will allow the network to be more dependable while simultaneously increasing capacity.
Additionally, there may be contamination. For instance, near Heathrow and other airports, aviation gasoline may be present in the atmosphere and may settle as a thin, lubricious layer.
CV: What are the advantages of using a plasma solution compared to traditional cleaning methods?
JS: To start with, PlasmaTrack technology does not use consumables. As a lighter and more compact system, we are much more environmentally friendly while also remaining efficient.
The system currently used in the UK is a high-powered water jetting system. There are around 62 of these devices placed on specific tracks that go throughout the UK rail network, which fail to clean all the rails.
Because the current system uses water, a precious resource, they tend to target the areas that are most affected or areas that have the biggest impact in terms of traffic. Consequently, you’ll find these jets scattered around areas, mostly around the Southeast, and much busier areas including Birmingham and Manchester.
Furthermore, the cost of these water jet systems to the Network Rail for the seasonal treatment is about £65m every year, not only for 10 weeks of the year. But the actual economic impact for the railway industry and for the UK in general circles around £355m per year.
Therefore, the size of the market is quite small in terms of the number of units, but the value is widespread. That is why it is very exciting for us if we can deliver those numbers and new pieces of equipment; the equipment they are currently using is, I believe, 25 years old, despite the fact that it was only intended to be about 20 years old.
The water jetting system must be updated, and it should be replaced with something more ecologically friendly, something that doesn’t consume as much fuel or has bad impacts on the water table and the ecosystem.
Our method consumes less fuel than a water jetting system because they currently require 200 million litres of water to do a seasonal treatment. Subsequently, there’s a lot of tonnage being moved across the rail network, as well as a lot of fuel merely to transfer the water, adding to this is the fuel-powered pumping mechanism.
We operate 50% quicker than the water jetting system, which operates at 40mph (64km/h) and can go up to 60mph (97km/h), allowing us to clean the whole track at a considerably faster pace.
CV: What does the future hold for PlasmaTrack?
JS: This is a period of extreme growth for us here at PlasmaTrack, we expect in the next year to potentially double if not triple our headcount into commercial activities.
This issue affects all rail operators. Therefore, part of our ambition is also not just to solve the UK challenge, but to branch out into Europe, North America, and the Far East sales.
We tend to work very closely with academia, and we are set on embarking on setting up a test lab with Derby University and expanding on our knowledge transfer partnerships with teams across various Universities.
Additionally, our involvement in developing the Raman Spectroscopy, a technique that allows you to measure materials, will give us more insight into the processes – which affect rail head-on.